Client: Aviation Industry
Location: United Kingdom
Project: Refurbishment of a foul water drywell submersible pumping station
Date: January 14, 2021
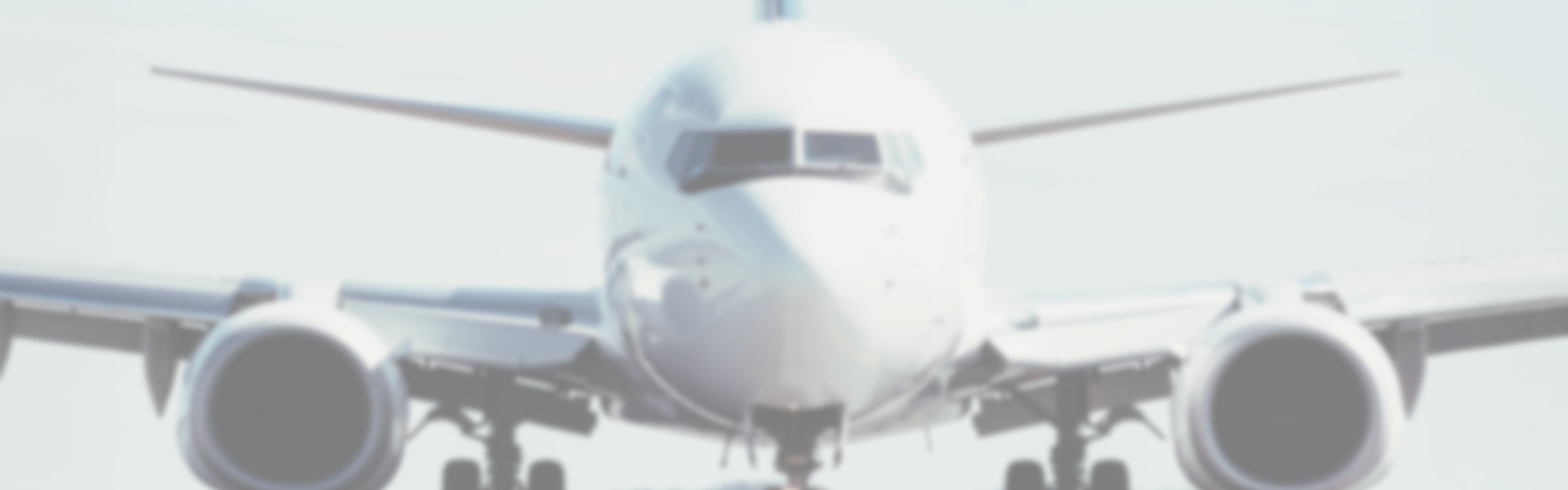
Submersible pumping station & Smart technology
AxFlow was commissioned to upgrade an aging foul water pumping station within the aviation sector. The existing system suffered from frequent breakdowns and maintenance challenges, particularly due to control panels located in confined spaces. The objective was to enhance reliability, safety, and operational efficiency without altering the station's structural framework.
Scope of works
Pump Replacement: Installed Flygt 3102 N-type submersible pumps equipped with screened cables suitable for Variable Speed Drive (VSD) applications.
Piping and Valves: Replaced air relief lines with black MDPE pipes and upgraded all isolation valves to resilient seat gate types. Non-return valves were updated to swing type with weight arms.
axflow.comControl Systems: Removed existing control panels from confined spaces and installed new Flygt SmartRun controllers with a central control unit in accessible areas. Retained the existing Milltronics Hydroranger level sensor, repositioning it alongside the new control equipment.
Flow Monitoring: Integrated a Xylem Magflux in-line magnetic flow meter on the common discharge pipe, with a remote display mounted outside the confined space.
Lighting and Safety: Upgraded lighting to LED fixtures with battery-backed emergency capabilities. Replaced the sump pump with a Lowara DOC3 unit, connected to a fixed 110V transformer located outside the confined area.
SCADA Integration: Prepared the system for potential full integration with the HEART (SCADA) system using MODBUS protocol for streamlined communication and monitoring.
Implementation Strategy
Given the continuous ingress of water and the necessity to maintain at least one operational pump throughout the refurbishment, AxFlow developed a phased approach:
Enabling Works:
Drained the sump and managed water ingress using a vacuum tanker.
Replaced suction valves and reconfigured high-level pipework to allow flexible connections.
Sequential Upgrades:
Executed replacements one leg at a time, ensuring uninterrupted pump operation.
Installed new controllers and alarm panels concurrently with mechanical upgrades.
Completed the integration of the Magflux flow meter and commissioned the SmartRun controllers.
Outcomes
Enhanced Efficiency
The Flygt SmartRun controllers optimize pump speed based on inflow, reducing energy consumption and minimizing start-stop cycles.
Improved Reliability
Automated cleaning cycles for the sump and pipes decrease the risk of blockages and maintenance requirements.
Operational Safety
Relocating control equipment out of confined spaces enhances accessibility and reduces health and safety risks.
Future-Ready Infrastructure
The system's compatibility with SCADA ensures scalability and advanced monitoring capabilities.